인도에 위치한 Wipro PARI는
세계적인 자동화 및 로봇 시스템 개발업체로
다임러, 마힌드라, 포드, FCA, 타타, 빈패스트, 르노닛산 및 PSA 그룹과 같은
글로벌 자동차 OEM사를 고객으로 두고 있는데요.
가공 및 파워트레인 부품 조립을 위한 다중 스테이션 라인을 포함하여
완전하고 자동화된 시스템을 설계, 제조 및 설치하고 있습니다.
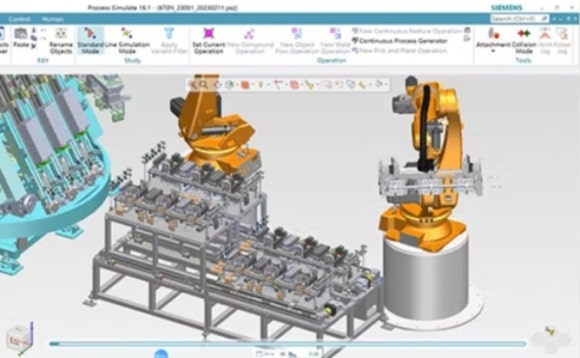
Wipro PARI는 가상 시운전(Virtual Commissioning) 프로세스를 통해
수작업 엔지니어링 노력을 줄이기 위해 노력했는데요.
가상 시운전 시뮬레이션을 활용하면
변경사항을 물리적으로 구현하기 전에 테스트를 위한 플랜트 디지털 트윈을 만들수 있고,
엔드 투 엔드 가상 검증, 기계 및 제어 시스템 설계,
위험 및 장애 모드 및 효과 분석을 수행할수 있어서
엔지니어는 비용 집약적인 재작업을 피할수 있습니다.
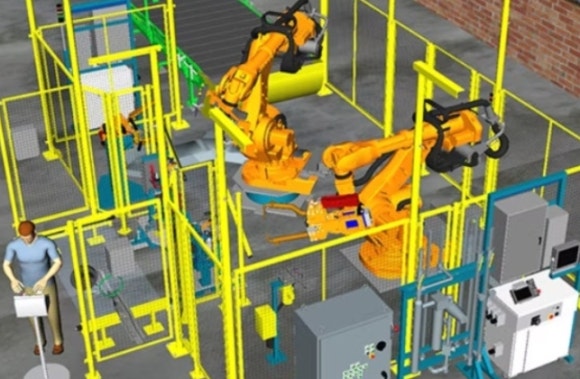
대규모 가공 라인에 대한 가상 시운전을 적용하기 위해
다양한 솔루션을 테스트 했는데요.
Tecnomatix 테크노매틱스 제품군 Process Simulate를 사용하면
가상 시운전을 하기 위한 포괄적인 디지털 트윈을 만드는데
가장 이상적인 솔루션이라는것을 확인했습니다.
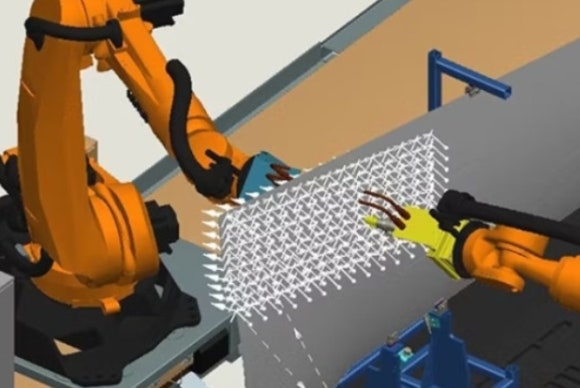
프로젝트 초기 과제는 OEM 제조 프로세스의 상당 규모를
처리하는 것이었는데요.
가공라인은 4개의 로봇과 10개의 가공 센터로 구성되었습니다.
세척, 디버링, 누출 테스트 및 비전 검사를 위한 기계와
100개 이상의 컨베이어, 슬라이드, 포지셔너, 리프터 및 부품 변형
그리고 라인 복잡성은 혼합 배치 모드에서 17가지 변형을 실행할 수 있다는 점에서 더욱 복잡해졌습니다.

대규모의 가상 시운전 프로젝트에 접근하기 위해
조립 라인을 4개 구역으로 나누고, Process Simulate를 실행했구요.
로봇을 위한 오프라인 프로그래밍(OLP) 통합과
맞품형 마크업 언어 XML을 수행해서 OLP에 필요에 맞게 기능을 향상시켰습니다.
그리고 안전한 중앙처리장치에 쓰여진 RFID, 비전 시스템 인터페이스,
스캐너 및 안전 로직을 시뮬레이션 했습니다.

그결과 재작업 시간을 50% 까지 최소화하고,
배송시간도 10% 단축을 했는데요.
가상 시운전을 통해 프로젝트 라이프사이클 초기에
모든 복잡한 사용 사례 및 장애 모드에 대한 장비 성능을 검증하고
최적화 할수 있었습니다.
이와 동시에 설계에서 작업장 시운전에 이르기까지
3개월만에 엔진 조립 라인에서 생산 볼륨을 높이는
또다른 가상 시운전 프로젝트를 완료했는데요.
정상적인 조건에서 6개월 이상 걸리던 것을
Process Simulate를 통해 절반으로 줄이는 놀라운 효과를 봤습니다.
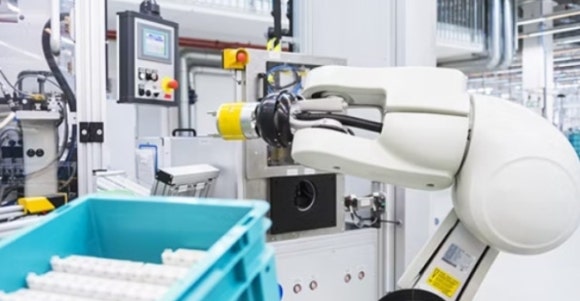
Wipro PARI는 Process Simalate 도입 후
현장 가상 시운전 시간을 70% 단축했으며,
단 3개월만에 가상 시운전을 통해 검증된 엔진 조립 라인을 만들수 있었습니다.
또한 재작업 시간을 50% 절감할수 있었으며,
공정 신뢰성 향상 등 다양한 효과를 볼수 있었습니다.
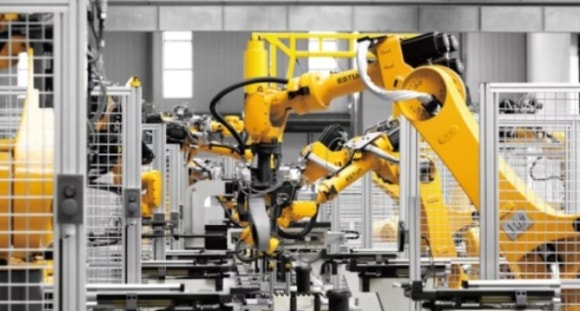
제조업 생존을 위해서 디지털 제조는 선택이 아닌 필수 입니다.
다양한 업종의 Tecnomatix 프로젝트 경험이 많은 당사와 함께하신다면
귀사의 경쟁력을 한단계 더 업그레이드 시킬수 있습니다.
아래 연락처로 연락주시면
귀사에 최적화된 디지털 제조 솔루션을 제안드리도록 하겠습니다.
H.P : 010-7901-5209
카카오톡 : choijh98