기계 및 설비는 실제 성형 과정에서 매우 중요한 기능을 담당하며,
생산 능력은 생산의 품질에 직접적인 영향을 주는데요.
사출 현장에서 CAE 엔지니어는 항상 CAE 소프트웨어 설정과
실제 사출 장비 사이의 인터페이스 차이가 크다는 어려운 문제가 있습니다.
그리고 런너 유량의 평형 문제로 인해 많은 금형 설계자들이
평형 유동 작용을 구현하는것이 항상 풀기 어려운 과제입니다.

사출성형해석 솔루션 Moldex3D는
시뮬레이션과 실제 제조 사이의 커뮤니케이션 채널을 성공적으로 구축했습니다.
성형 조건 마법사는 각종 사출 장치의 특성을 지원하며,
사출 성형 해석에서 활용할수 있는데요.
조건 설정 완료 후 분석하고 간편하게 실제 장치 인터페이스로 전환이 가능합니다.

또한 런너 응용에 있어서 용융 유동, 압력 강하, 열 발생 차단 영향 및
금형 온도 동향 분포 등을 분석할수 있으며,
복잡한 핫 런너 시스템을 이해하는데 매우 유용합니다.
그래서 잠재적인 문제를 발견하는데 많은 도움이 되며,
효과적인 핫 런너 시스템 설계를 개선해서 제품 품질을 높이는 동시에
실제 금형 테스트 횟수, 비용, 그리고 개발 시간을 줄여줄수 있습니다.

사출성형해석 솔루션 Moldex3D는
각종 사출기의 스틱 직경 or 사출 압력과 같은 특성을 광범위하게 지원하며,
실제 성형 장치 조작 페이지에서 입력 기기 충전 속도 및 압력 반응을 제공해서
시뮬레이션의 정확도를 높일수 있습니다.

수십년간 에너지 절감 모터의 핵심 기술 개발에 전념하고 있는 A사는
Moldex3D의 고급 핫 런너 모듈 분석을 통해
콜드 슬러그 위치를 발견했으며, 사출 시 불안정함과 압력 이상을 발생하는
원인을 파악할수 있었습니다.
그 결과 핫 런너 압력은 50%까지 낮아졌고, 안정성이 향상되었으며
유로 온도 분포를 개선하면 성형 효율을 효과적으로 높일수 있음을 증명했습니다.

세계 최대 자동차 충돌 대체 부품 제조업체 B사는
Moldex3D를 활용해서
제품 외관의 웰드 라인 및 에어 트랩 결함을 효과적으로 해결했으며,
여러 차례의 몰드 재작업 비용 방지 그리고 설계 결정 간소화 등
다양한 효과를 보았습니다.

한국의 선도적인 플라스틱 가공 원료 제조업체 C사는
Moldex3D 냉각 해석을 활용해서 냉각 시간을 85초 -> 28초로 단축했으며,
기계 모드 인터페이스를 통해 시뮬레이션 분석을 실제 제조에 더욱 근접시킬수 있었습니다.
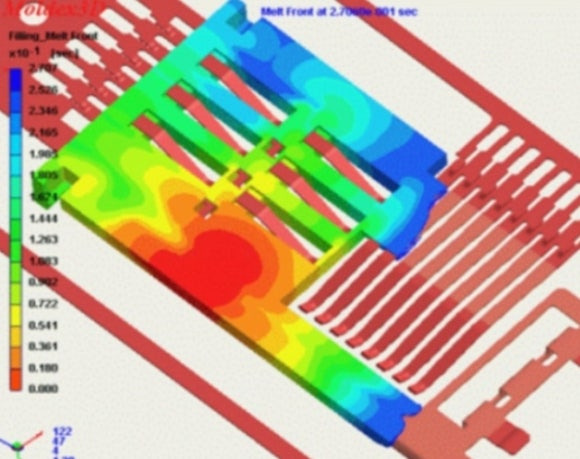
당사는 오랜기간동안 다양한 업종과 제조기업을 대상으로
Moldex3D 플라스틱 사출성형해석 솔루션을 공급하고,
다양한 프로젝트 경험이 있는데요.
아래 연락처로 연락주시면
귀사에 최적화된 Moldex3D 사출성형해석 솔루션을 제안드리도록 하겠습니다.
